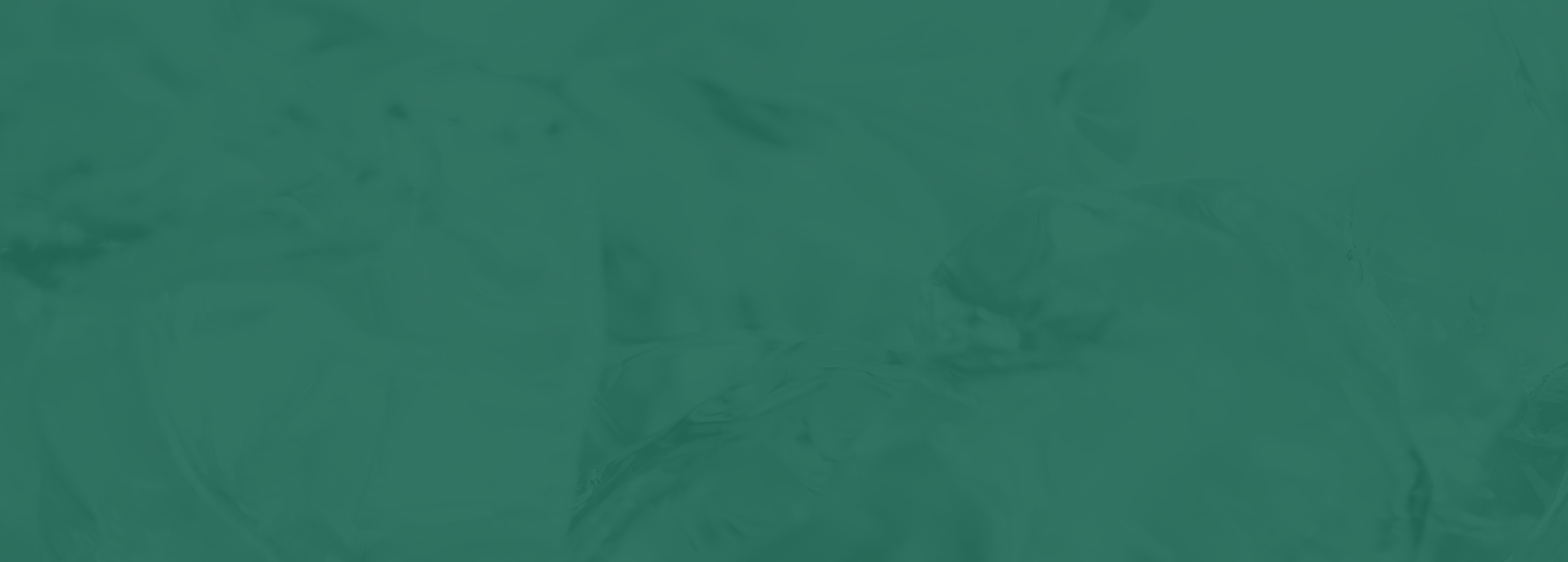
Food & Beverage Kikkoman
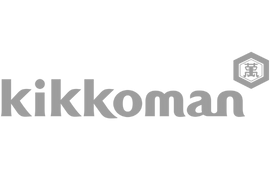
Challenge
In its current form, Soy Sauce was created about 2,200 years ago in ancient China and spread throughout East and Southeast Asia, where it is used in cooking and as a condiment. Today, a staple in East Asian cuisines, soy sauce is the third most popular condiment in the United States, and due to its viscosity, it is the hardest to contain. Traditionally shipped in a semi-rigid plastic cube that delivers erected in boxes, the soy sauce industry was interested in shifting towards a container that saved on transportation costs, eliminated the fluorination treatment for barrier protection, ensure the product arrives at the destination securely and reduced the foaming of the product during the filling stage.
Solution
Kikkoman would have to bring in full truckload quantities of the semi-rigid plastic cube package, inflated and assembled, which equals 3,000 containers. Eager to reduce their transportation costs and maximize their warehouse storage, Kikkoman needed a package that shipped flat. The Cheertainer® Bag-in-Box exceeded this need by delivering 72,000 bags per truckload, and because they ship flat, this reduced the amount of space required in the warehouse.
The traditional soy sauce package shipped in an erected state because it had to undergo a fluorination treatment before filling. Fluorination creates a barrier between the plastic and the product, preventing the soy sauce smell from permeating the package. Fluorination is an expensive process and could be eliminated with the selection of the correct film combinations. After conducting shelf-life holding studies on a few different film combinations, it was determined that a medium barrier liner would efficiently meet barrier requirements.
The primary mode of transporting the filled product was by rail. The soy sauce company expressed concerns around flex cracking in the bag, and due to the viscosity of the product, experiencing leaks. CDF packaged a pallet of soy sauce in the standard bag and box and shipped the pallet the regular rail route. The top layer of bag-in-boxes experienced flex cracking. CDF recreated the rail experience by palletizing the same amount of soy sauce in the standard bag and box package and putting the pallet through vibration table trials. Our engineers observed the vibration testing and were able to identify movement in the bag that was causing cracking. By making small changes in the structure of the bag and adjusting the box’s orientation, we eliminated the flex cracking issue.
Kikkoman was experiencing foaming with their filling equipment, and due to the foaming, they had to slow down their filling process, which translated into fewer fills per minute. Kikkoman liked our filling equipment, partnership with the manufacturer, Flexifill, and post-installation service and support. By converting them to the Flexifill machine and the Cheertainer bag-in-box solution, they could increase throughput and eliminate product foaming.
Results
By working closely with the CDF team, Kikkoman eliminated the added cost of the fluorination stage, which led to lesser transportation costs and logistical concerns, ensuring the product arrived securely to their end-user without compromising the filling speeds of the product.
Get In Touch
We’d love to hear how we can work with your company to develop solutions, field your questions, or meet inspiring people like you to join our team.